QUALITÄTSKONTROLLE ALUMINIUM
EINFÜHRUNG
Symbol: Al
Ordnungszahl: 13
Dichte: 2,7
Molare Masse: 27 g.mol-1
Schmelzpunkt: 660 °C
Aluminium wird in mehreren Stufen hergestellt:
• Zunächst erfolgt die Gewinnung des Bauxit-Erzes (enthält 60% Aluminiumoxid Al2O3, 20-30% Eisenoxid Fe2O3 und Siliziumoxid SiO2 und Titanoxid TiO2 in geringeren Mengen).
• Das Bauxit wird dann unter Verwendung von Natronlauge bei hoher Temperatur und unter hohem Druck in Aluminiumoxid umgewandelt.
• Das zuvor erhaltene Aluminiumoxid wird in einem Kryolithbad gelöst und ein elektrischer Strom wird durch den Tank geleitet. Dieser als Elektrolyse bekannte Vorgang ermöglicht das Sammeln von Aluminium an der Kathode.
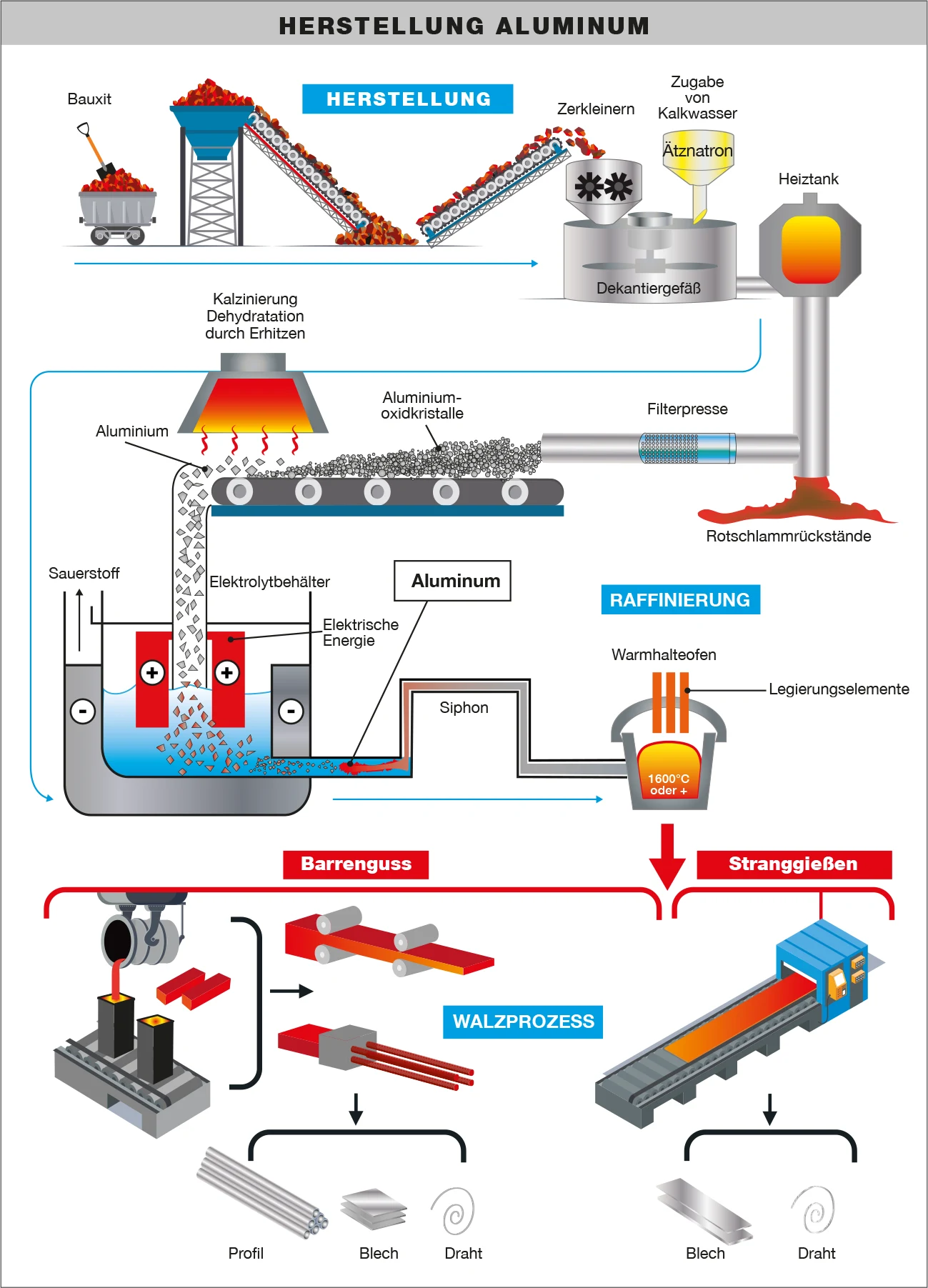
Abb. 1: Aluminiumverarbeitung
Legierungselemente werden verwendet, um die Eigenschaften von Aluminium zu verbessern:
• Magnesium verbessert die Korrosionsbeständigkeit
• Silizium erhöht die Formbarkeit der Legierung in der Gießerei
• Kupfer härtet Aluminium aus
• Zink und Mangan sind ebenfalls wichtige zusätzliche Elemente bei der Herstellung von Aluminiumlegierungen
Es gibt zwei Hauptfamilien von Aluminium:
Der am häufigsten verwendete Name für Aluminium-Schmiedeeisen ist eine 4-stellige Referenz (NF EN 573-1), der EN AW vorangestellt ist.
Die erste Ziffer bestimmt die Legierungsgruppe, zu der das Aluminium gehört.
Die 2. Ziffer für Gruppe 1 entspricht den im Aluminium enthaltenen Verunreinigungen.
Die 2. Ziffer für die anderen Gruppen entspricht Änderungen der chemischen Zusammensetzung der Legierung.
Die 3. und 4. Stelle für Legierungen der Gruppe 1 geben den Prozentsatz über 99% und für die anderen Gruppen eine Legierung in ihrer Gruppe an.
Beispiel: EN AW – 2024 ist eine Aluminiumlegierung mit 4% Kupfer und 1,5% Magnesium. (Das W (geschmiedet) bezieht sich auf eine Knetlegierung).
Gruppe | Aluminium und Aluminiumlegierungen |
1 | Aluminium (Anteil ≥ 99.00%) |
2 | Aluminium – Kupfer |
3 | Aluminium – Magnesium |
4 | Aluminium – Silizium |
5 | Aluminium – Magnesium |
6 | Aluminium – Magnesium – Silizium |
7 | Aluminium – Zink |
8 | Andere Aluminiumlegierungen |
Tabelle 1: Aluminiumlegierungsgruppen
Der von der Gießerei vergebene Name des Aluminiums bezieht sich auf die Normen NF EN 1780-1, -2 und -3.
Die numerische Identifikation besteht aus einer Reihe von 5 Ziffern, von denen sich die erste auf Tabelle 1 der Knetlegierungen bezieht. Die letzten 3 Ziffern geben die chemische Zusammensetzung der Legierung an.
Schließlich gibt die Norm NF EN 1706 die Grenze der chemischen Zusammensetzung jeder Legierung sowie die mechanischen Eigenschaften dieser Gusslegierungen an.
OBERFLÄCHENBEHANDLUNGEN VON ALUMINIUM
Einige Aluminiumlegierungen wurden speziell für diese Behandlung entwickelt und die Anodisierungsdicke kann im Bereich von 5 bis 50μm liegen. Diese Oberflächenbehandlung verbessert die Korrosionsbeständigkeit und wird auch für ästhetische Zwecke verwendet.
VORTEILE UND ANWENDUNGEN VON ALUMINIUM UND SEINEN LEGIERUNGEN
• Mechanische Beständigkeit: Dies wird durch die Zugabe von Legierungszusätzen zum Aluminium verbessert.
• Korrosionsbeständigkeit: Auf Aluminium bildet sich auf natürliche Weise eine Oxidschicht, die es vor Korrosion schützt. Die anodisierende Oberflächenbehandlung kann die Korrosionsbeständigkeit weiter verbessern.
• Sehr gute thermische und elektrische Leitfähigkeit: Aus diesem Grund wird Aluminium häufig für Wärmeableitungsanwendungen verwendet. Die elektrische Leitfähigkeit von Aluminium beträgt 65% der von Kupfer.
• Leichtigkeit: Diese Eigenschaft wird besonders in der Luft- und Raumfahrt geschätzt und ist in diesen Bereichen sehr wichtig.
• Undurchlässigkeit: Aluminium lässt kein Licht, keine Gerüche oder Mikroorganismen durch. Aus diesem Grund wird es für Lebensmittel- und Pharmaverpackungen verwendet.
Aluminium wird in der Luft- und Raumfahrt sowie in der Automobilindustrie eingesetzt.
Aluminium ist auch in der Lebensmittel- und Pharmaindustrie weit verbreitet.
Im Bausektor wird Aluminium häufig zur Herstellung von Fenstern, Erkerfenstern, Profilen an Außenfassaden usw. verwendet.
METALLOGRAPHISCHE PRÄPARATION
Diese Schritte sind in der folgenden Reihenfolge:
• Standardisierung der Geometrie der entnommenen Probe (falls erforderlich), genannt «EINBETTEN».
• Verbesserung des Oberflächenzustands dieser Probe, genannt «SCHLEIFEN & POLIEREN».
• Charakterisierung der Probe: Aufdecken der Mikrostruktur der Probe durch ein Ätzreagenz (falls erforderlich) namens «ÄTZEN» und mikroskopische Untersuchungen (optisch oder elektronisch).
TRENNEN
Das breite Angebot von PRESI an Trenn- und Präzisionstrennmaschinen mit mittlerer und großer Trenn-Kapazität kann an alle Anforderungen hinsichtlich Schnittgenauigkeit, Dimensionierung oder Menge der zu schneidenden Produkte angepasst werden:
Abb. 4: Spannen eines Turboladers – EVO 400
Abb. 5: Spannen eines Wärmetauschers – ST310
Abb. 6: Profilspannung – T330
Abb. 7: Spannen einer Nockenwelle – T210
In den vorherigen Abbildungen werden je nach Geometrie der zu trennenden Teile unterschiedliche Spannmöglichkeiten aufgezeigt. In den vorliegenden Fällen wurden Kopal-Spanner und Schnellspannschraubstöcke verwendet. Alle diese Spannmittel können an die verschiedenen Trennmaschinen angepasst werden (in den obigen Beispielen: Mecatome ST310, EVO 400 und Mecatome T330 oder Mecatome T210).
VERBRAUCHSMATERIAL
ALUMINIUM UND SEINE LEGIERUNGEN | |
Präzisionstrennen | MNF UTW S (Ø 180mm) C |
Trennen mittelgroßer Proben | MNF |
Trennen großer Proben | MNF |
Tabelle 2: Auswahl der richtigen Trennscheibe
EINBETTEN
Das Erreichen einer qualitativ hochwertigen Einbettung ist wichtig, um zerbrechliche Materialien zu schützen und gute Präparationsergebnisse für das Polieren und zukünftige Analysen zu erzielen.
Vor der Einbettung sollte die Probe gesäubert werden und Schneidgrate sind zu entfernen. Eine Reinigung mit Ethanol und in einem Ultraschallbad ist ebenfalls möglich. Dies ermöglicht es dem Harz, so gut wie möglich an der Probe zu haften und reduziert somit die Schrumpfung (Raum zwischen dem Harz und der Probe).
Wenn eine Schrumpf vorherrscht, kann dies zu Problemen beim Polieren führen. Schleifkörner können sich in diesem Raum festsetzen und zu einem späteren Zeitpunkt freigesetzt werden, wodurch die Gefahr von Kratzern auf der Probe und der Polierfläche besteht. In diesem Fall wird empfohlen, zwischen den einzelnen Schritten die Probe in ein Ultraschallgerät zu legen.
Es gibt zwei Einbettmöglichkeiten:
DIE WARMEINBETTUNG
• Vollautomatische Warmeinbettpresse.
• Einfach zu bedienen
• Ihr Speicher, Ihre Prozessanpassung und ihre Ausführungsgeschwindigkeit machen Sie zu einer hochpräzisen Maschine.
• Die Warmeinbettmaschine hat 6 verschiedene Formdurchmesser von 25.4-50 mm.
PLUSPUNKT
KALTEINBETTUNG
• Wenn die zu untersuchenden Teile zerbrechlich / druckempfindlich sind
• Wenn sie eine komplexe Geometrie haben, z. B. eine Wabenstruktur.
• Wenn eine große Anzahl von Teilen in Serie eingebettet werden soll.
Das Kalteinbettverfahren kann angewendet werden mit:
PLUSPUNKT
PLUSPUNKT
VERBRAUCHSMATERIAL
Die Kalteinbettung ist auch flexibler als die Warmeinbettung, weil es unterschiedliche Einbettformen für spezifische Anforderungen gibt.
ALUMINIUM UND SEINE LEGIERUNGEN | |
Warmeinbettprozess | Phenol Allyl |
Kalteinbettprozess | KM-U 2S IP |
Tabelle 3: Auswahl des richtigen Einbettmittels
Wenn die harte Eloxalschicht untersucht werden soll, sollte die Probe unter Verwendung eines schrumpfarmen Einbettmittels eingebettet werden, um die Eloxalschicht so gut wie möglich analysieren zu können.
SCHLEIFEN UND POLIEREN
PRESI bietet eine breite Palette an manuellen und automatischen Schleif- und Poliermaschinen an, mit einer großen Auswahl an Zubehör für alle Anforderungen, vom Schleifen bis zum Superfinish und Polieren von Einzel- oder Serienproben.
Die MECATECH-Reihe von automatischen Schleif- und Poliermaschinen ermöglicht es sowohl manuell als auch automatisch zu Schleifen und Polieren. Mit seinen fortschrittlichen Technologien und einer Motorleistung von 750 bis 1500 W konzentriert sich die gesamte Erfahrung von PRESI auf dieses sehr vollständige Sortiment. Unabhängig von Probenanzahl oder -größe garantiert die MECATECH ein optimales Schleif- oder Polierergebnis.
VERBRAUCHSMATERIAL UND POLIERANLEITUNGEN
Alle ersten Schritte jeder Polieranleitung werden als «Nivellieren» bezeichnet und bestehen darin, Material schnell zu entfernen, um eine plane Oberfläche der Probe (und des Einbettmittels) zu erhalten. Die unten angegebenen Parameter sind Standard und können daher nach Bedarf geändert werden.
Der Probenandruck variiert je nach Probengröße, im Allgemeinen gilt jedoch Folgendes: 1 daN pro 10 mm Einbettdurchmesser für die Schleifschritte (z. B. Ø 40 mm = 4 daN), dann die Kraft bei jedem Polierschritt mit einer Schleifsuspension um 0,5 daN reduzieren.
Das Folgende ist ein allgemeiner Polierprozess für Aluminium und seine Legierungen:
POLIERPROZESS N°1
N° | Verbrauchsmaterial | Suspension / Lubrikant | Arbeitsplatte (U/min) | Kopf (U/min) | Rotationsrichtung von Arbeitsplatte / Kopf | Zeit (mm) |
1 | P320 | Wasser / Ø | 300 | 150 | 1’ | |
2 | TOP | 9μm LDM / Reflex Lub | 150 | 135 | 4’ | |
3 | RAM | 3μm LDM / Reflex Lub | 150 | 135 | 3’ | |
4 | NT | 1μm LDM / Reflex Lub | 150 | 135 | 1’ | |
5 | SUPRA | SPM / Wasser | 150 | 100 | 1’ |
Beim Schleifen sollte die Drehrichtung des Kopfes und der Platte nicht entgegengesetzt werden, da dies die Planheit beeinträchtigen kann. Das Umkehren der Drehrichtungen kann jedoch hilfreich sein, wenn eine große Menge Material entfernt werden muss.
Das Diamantpolieren kann unter Verwendung einer monokristallinen Diamantsuspension durchgeführt werden. Im Allgemeinen funktioniert aber auch eine polykristalline Diamantsuspension (achten Sie auf mögliche abrasive Partikel, die im Aluminium stecken bleiben können). Dies kann im Fall einer Verbrauchsmaterial-Optimierung nützlich sein, wenn nicht nur Aluminium poliert werden muss.
Wenn Diamanten durch die Politur in das Material eingebettet werden, sollte es mit der monokristallinen Diamantsuspension poliert werden.
Ein zweiter Polierprozess kann zum Polieren von Aluminium und seinen Legierungen verwendet werden:
POLIERPROZESS N°2
N° | Verbrauchsmaterial | Suspension / Lubrikant | Arbeitsplatte (U/min) | Kopf (U/min) | Rotationsrichtung von Arbeitsplatte / Kopf | Zeit (mm) |
1 | P320 | Wasser / Ø | 300 | 150 | 1’ | |
2 | MED-R | 9μm Diamond MED R / Ø | 150 | 135 | 4’ | |
3 | RAM | 3μm LDP / Reflex Lub | 150 | 135 | 3’ | |
4 | NT | 1μm LDP / Reflex Lub | 150 | 135 | 1’ | |
5 | SUPRA | SPM / Wasser | 150 | 100 | 1’ |
Auf diesem Träger wird eine speziell für MED-R entwickelte Diamantsuspension verwendet. Diese Aufhängung kombiniert Diamant und Schmiermittel.
Bei Schweißnahtprüfungen entspricht ein dritter Polierprozess speziell dieser Art der Prüfung.
POLIERPROZESS N°3
N° | Verbrauchsmaterial | Suspension / Lubrikant | Arbeitsplatte (U/min) | Kopf (U/min) | Rotationsrichtung von Arbeitsplatte / Kopf | Zeit (mm) |
1 | P320 | Wasser / Ø | 300 | 150 | 1’ | |
2 | TOP | 9μm Gel 2+ poly / Ø | 150 | 135 | 4’ | |
3 | ADR II | 3μm Gel 2+ poly / Ø | 150 | 135 | 3’ |
MIKROSTRUKTUR
DOWNLOAD DER LABORNOTIZ
Füllen Sie einfach das untenstehende Formular aus:
Entdecken Sie unsere anderen Lab’Note:
- Qualitätskontrolle 3D-druck
- Kontrolle Wärmebehandlung abgeschreckt
- Qualitätskontrolle Medizinprodukte
- Qualitätskontrolle Stahl
- Qualitätskontrolle Edelstahl
- Qualitätskontrolle Gusseisen
- Qualitätskontrolle Kupferlegierung
- Qualitätskontrolle Aluminium
- Qualitätskontrolle Titan
- Qualitätskontrolle Keramikwerkstoffe
- Qualitätskontrolle Elektrobauteile
- Qualitätskontrolle Edelmetall